“Print Basics” is a series that provides an in-depth look at print, prepress, ink and more.
In the previous post, we looked at an overview of print and the two main types of print processes for envelopes – flexography and offset lithography. Let’s take a deeper look into what has been called the “envelope workhorse,” flexography.
What is Flexography?
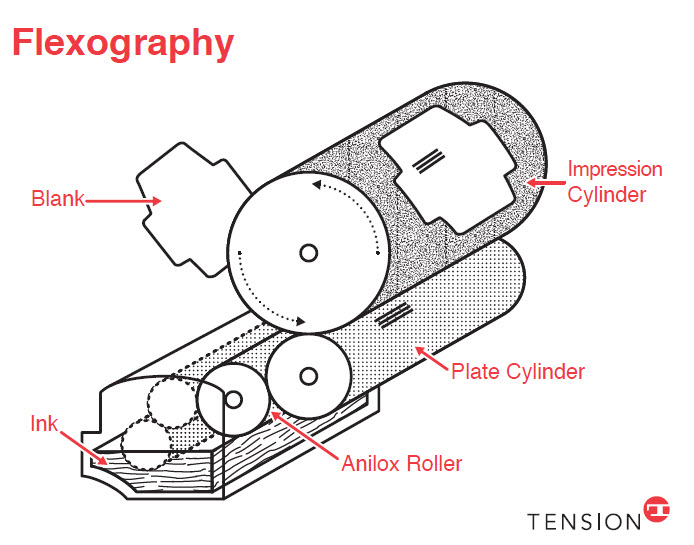
Flexography, or flexo for short, is a form of printing that uses a flexible plate made of rubber or photopolymer materials, rubber fountain rollers, an anilox, or hard cylinder with a steel or aluminum core and coated with a ceramic surface engraved with fine dimples, roll inking system and fast-drying water-based inks.
How Flexography Works
Flexo is a type of printing that transfers ink to a substrate, such as paper, by way of a flexible plate:
- The fountain roller rotates in an ink reservoir and transfers it to the anilox roller.
- The anilox roller has an engraved surface that holds a certain amount of ink and allows the remainder to drip back into the fountain.
- The anilox roller then turns against the plate cylinder, which holds the flexible plate with the two-dimensional design and applies ink to raised surfaces on the plate.
- The plate rotates against the envelope paper on the impression cylinder and applies or stamps the ink directly to it in a series of small dots.
- The end result is an image made up of dots that fools the eye and brain into seeing a complete, tonal image.
Benefits of Flexography
Most envelopes are printed with the flexographic process, and it is typically done during the manufacturing process on a web fed machine.
Because flexo printed envelopes are converted on web fed machines, they offer the least expensive and simplest printing method. Additionally, many flexo printing systems feature a doctor blade ink system, which works to remove excess ink from the anilox roller in order to have a more superior printing job.
Three Types of Flexography
Commonly, flexo is ideal for one- or two-color print jobs, such as transactional envelopes. There are various configurations in envelope production for flexo applications, and some allow for more color options:
- Stacked – A stacked flexography process refers to when two or three printing units are placed vertically in stacks. Each printing unit holds one color, so more are added to allow for more color options.
- Inline – Inline refers to individual print stations that are placed sequentially along a web path with the individual colors in each station needed to produce the imagery.
Tip: A narrow web inline press is another flexo option that allows the use of special UV inks or foil, allowing for big improvements in print quality and enabling flexo to approach lithographic-quality print.
- Central Impression – Central Impression Flexo, or Enhanced Flexo, offers more elaborate and higher-quality images. It is typically used for 4-color process (CMYK) imagery, and it uses a central impression print cylinder to achieve tighter print registration along with four ceramic anilox rollers and four ink reservoirs. Enhanced Flexo uses digital plates to achieve finer screens and print resolution on calendarized papers. Direct mail projects with lots of color, text and imagery are often ideal candidates for Enhanced Flexo print.
Flexographic Printing with Tension
How well do you know flexo, the envelope workhorse? Contact us today and let’s discuss how flexography can benefit your project.